Your
Success Begins with Quality Training and Education |
(615)
924-3600 |
|
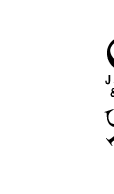 |
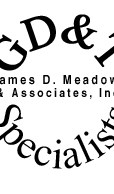 |
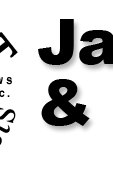 |
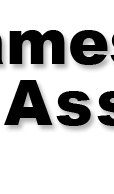 |
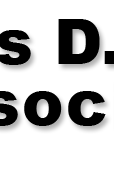 |
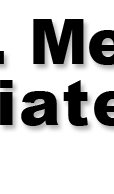 |
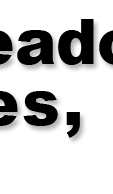 |
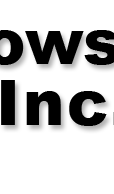 |
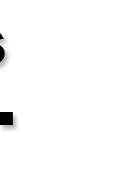 |
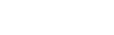 |
|
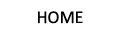 |
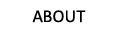 |
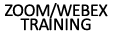 |
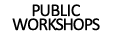 |
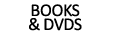 |
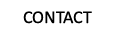 |
|
 |
|
New Textbook
GEOMETRIC DIMENSIONING AND TOLERANCING
Applications, Analysis & Measurement [per
ASME Y14.5-2018]
|
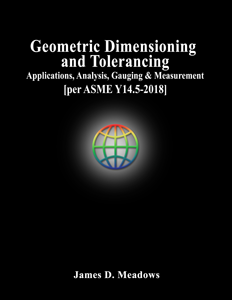 |
|
James D. Meadows
© May, 2019
Co-published
by ASME
576 pages, hardcover, illustrated
ISBN: 978- 0- 578- 47048- 1
Publisher Price: $131
Geometric Dimensioning and Tolerancing – Applications, Analysis
& Measurement [per ASME Y14.5-2018] is based on the ASME
Y14.5- 2018 Dimensioning and Tolerancing Standard.
This textbook reflects new symbology, rules and basic principle
revisions that are contained in ASME Y14.5- 2018. It shows
how to interpret design drawings and CAD representations
of product definitions that use the ASME Y14.5- 2018 standard.
It also explains step- by- step procedures to apply the new
Y14.5- 2018 practices and allows dimensioning and tolerancing
professionals to express their design requirements more
clearly. The results are that: requirements are more specific
in conveying functional tolerancing needs, products can
be more easily manufactured, and appropriate inspection
techniques are clarified. |
|
|
This is one of the most comprehensive
GD&T textbooks ever written by a single author. Some of
the concepts covered in this text are: |
|
|
-
All of the new symbols, rules and
principles instituted by the ASME Y14.5 - 2018 Standard
-
Basic GD&T
-
Advanced GD&T
-
Tolerance Stack- Up Analysis
-
Statistical Tolerancing
|
-
Inspection Techniques and Sources
of Measurement Uncertainty
-
Gage and Fixture Design
-
Tolerancing Mating Parts and Assemblies
-
Analyzing and Correcting Interferences,
Imbalance in Rotating Parts and Material Strength Problems
due to Insufficient Wall Thickness
|
Textbook Contents:
|
1 Symbols,
Rules, Charts
- Geometric Characteristics
- Symbols
- New Symbols
- Old Symbols, New Meanings
- Charts- Food Chains of Symbology
- A Few Basic Definitions, Formulas and Guidelines
- New Rule Regarding the Use of Regardless of Feature Size
- Maximum Material Boundary, Least Material Boundary and
Regardless of Material Boundary
- Actual Minimum Material Envelope vs. Actual Mating Envelope
- Flatness of the Derived Median Plane
- Types of Controls
- Tolerances
- General Rules for Tolerances
2 Selecting a Tolerancing Approach
- Datums and Datum Features
- Defining, Tolerancing and Qualifying Datum Features
- Fixed Fastener Assembly Tolerancing Formula
- Simultaneous Requirement Rule
- Reading a Feature Control Frame
3 Datum Feature Simulators and True Geometric Counterparts
- Datum Feature Simulators: and True Geometric Counterparts
- Fixtures, Gages and Virtual Condition Boundaries
4 Boundaries and Material Condition Symbols, MMC, LMC & RFS
- Dimensioning and Tolerancing Overview
- Rule #1: Size Tolerance and Form Tolerance are Interdependent
- Exceptions to Rule #1
- Principle of Independency Symbol
- GO Gages
- Brief Comparison of Concentricity, Circular Runout, Total Runout
and Position Tolerancing
- Introduction of Orientation on Mating Parts
- Material Condition Symbols and Concepts Explained
- Regardless of Feature Size
- Least Material Condition
- Maximum Material Condition
- Inner and Outer Boundary Calculations
5 Major Concepts of Geometric Dimensioning and Tolerancing
- Converting from Plus and Minus Tolerance to Geometric Tolerance
- Position
- Profile
- Selecting Datum Features
- Size Tolerance Controls Form Tolerance (Rule #1), GO Gages
- Flatness
- Perpendicularity
- Mating Part Tolerancing
- Reading the Feature Control Frames as a Language
- Functional Gages
- Calculating Inner and Outer Boundaries
- Virtual Condition
- Resultant Condition
- Practical Absolute Gage Tolerancing
- Bonus Tolerancing Formulas
- Allowed vs. Actual Deviation from True Position Calculations
- Conversion Chart Inches
- Conversion Chart Millimeters
- Tolerance Zone vs. Boundary Verification
- Another Difference between Bonus Tolerance (Growth) and Datum
Shift
(Movement) of Tolerance Zones
6 Form
- Flatness
- Straightness
- Cylindricity
- Circularity (Roundness)
- Spherical Diameters Controlled with Circularity
- Average Dimensions
7 Orientation
- Parallelism
- Parallelism of a Tangent Plane
- Perpendicularity
- Angularity
- Angularity of a Tangent Plane
- Angularity as a Refinement of Position
- Shifting vs. Growing Tolerance Zones
8 Profile
- Profile of a Surface
- New Symbol for Unequal or Unilateral Profile Tolerancing
- NONUNIFORM Profile
- Dynamic Profile
- Profile of a Line
- The Power and Versatility of Profile (Mating Parts)
- Tolerancing Mating Part Profiles
- Composite Profile
- Composite vs. Two Single Segment Profile Controls
- Profiling Patterns of Features Using 3 Levels of Profile Tolerances
- Coplanarity
- Continuous Feature of Size Symbol
- Dimension Origin Symbol
- Locating Offset Surface with Profile of a Surface
- Conicity
9 Runout
- Circular Runout
- Total Runout
- Comparison of Perpendicularity and Total Runout on a Planar
Surface
10 Concentricity and Symmetry [per ASME Y14.5- 2009]
- Concentricity
- Comparison of Coaxiality Controls
- Symmetry
- Symmetrical Part Symbol
11 Datums
- How They are Selected and What They Mean
- Specifying Degrees of Freedom
- Datum Feature Simulation
- Designating Degrees of Freedom on the Part Drawing
- Establishing a Valid Datum Plane
- Effects of Differing Datum Precedence on Part Acceptance
- Curved Surface as a Datum Feature
- Conical Datum Features
- Datum Feature Pattern Referenced Regardless of Material Boundary
- Inclined Datum Feature
- Constant Cross- Sections and Complex Datum Features
- Specifying Degrees of Freedom in the Feature Control Frame
- Multiple Datum Reference Frame Identification
- Correct Material Boundary Size Specified Next to the Datum
Feature
- Correct Material Boundary Calculations
- Using the Translation Modifier
- Basic or BSC Spelled Out in a Feature Control Frame
- Planar Datum Feature Simulated at Regardless of Material Boundary
(RMB)
- Planar Datum Feature Simulated at Maximum Material Boundary
(MMB)
- Offset Datum Features of Size Simulated at RMB and MMB
- Profiled Datum Features Simulated at RMB and MMB
- Irregular Datum Features of Size
- Repetitive Patterns
12 Centerplane Datums
- An Overview
- Centerplane Datums on Mating Parts in a Fixed Fastener Assembly
13 Position with Fixed Fastener Assemblies and Projected Tolerance Zones
- Tolerancing Mating Parts in a Fixed Fastener Assembly
- Projected Tolerance Zones and How they are Measured
- Datum Feature Shift/Pattern Shift
- Alternate Method Using Chain Lines to Show Projected Tolerance
Zones
- Calculating Clearance Hole Sizes Needed Without Projected Tolerance
Zones
- Alternate Method Using Chain Lines to Show Projected Tolerance
Zones |
|
14 Tolerancing Mating Parts in a Floating
Fastener Assembly
- Floating Fastener Assembly Condition (Radial Hole Patterns)
- Assigning Datum Features to Mating Parts with Radial Hole Patterns
- Calculating Position Tolerance
- Two Single Segment Position Tolerancing
- Calculating Minimum Wall Thicknesses
- Accumulative Datum Shift on Mating Parts in an Assembly
- Tolerance Zones and Their Movement with Two Single Segment
Position
15 Direct vs. Indirect Relationships
- Overview
- Tolerancing Mating Parts Holding Function Directly and Indirectly
- Switching Datums in Mid- Stream
- Unique Effects of Utilizing the LMC and LMB Concepts
- Wall Thickness Calculations
16 Datum Targets
- Flexible Parts, Datum Targets and Partial Datum Features
- Sheet Metal Panels and GD&T Sheets
- Equalizing Datums
- Moveable Targets, Finding the Datum Planes and Fixturing
- Vector Symbols
- Datum Target Symbols for Spherical Diameters
- Centerplane Datums
- Spherical Tolerance Zones
17 Datum Feature Scheme Choices
- Datum Feature Patterns and Profile
- Simultaneous Requirements
- Compound Datum Features of Size
- Secondary and Tertiary Datum Features of Size
- Finished Machining Requirements for a Cast Part
18 Flexible Parts
- Flexible Parts and Inspecting Them in the Way They Work
- Temporary Datum Features
- Common Misconceptions
- Free State Variation in Sheet Metal Parts
- Specifying Restrained State Inspection
- Fixturing Sheet Metal Parts
- Profile ALL OVER Controls and What They Mean
19 Position Boundary Concept
- Position Boundary
- Elongated Holes
- Functional Gages and Virtual Condition Boundaries
- Tolerancing Hoses, Pipes and Tubing with Positional Boundary
- Tolerancing Oddly Configured Features with Positional Boundary
- Oddly Configured Datum Features and How to Represent them in
Gages
- Tolerance Zones vs. Boundary Concept Explanation
- Rectangular Tolerance Zones for Round Holes
- Bi- directional Position Tolerancing, Polar Coordinate Method
20 Why Use GD&T
- Multiple Interpretations of Simple Plus and Minus Tolerances
- Converting from Plus and Minus to Composite Position Tolerancing
- Calculating the Position Tolerance for a Composite Position
Control
- Minimum Wall Thickness Calculation for Composite Position Tolerances
- Composite Tolerancing for Coaxial Hole Patterns
- Minimum Wall Thickness Calculations for Coaxial Hole Patterns
- Composite Position Tolerancing with 3 Levels of Control
- Differentiating Between Features of Similar Size and Shape
21 Composite vs. Two Single Segment Positional Tolerancing
- Composite vs. Two Single Segment Positional Tolerancing
- Similarities
- Differences
- One Level Tolerancing vs. Composite Tol. and Simultaneous Requirements
- Two Single Segment Position Controls
- Refining Geometric Controls to be More Cost Effective
22 Dimensioning and Tolerancing of Gages
- Dimensioning and Tolerancing of Gages per ASME Y14.43- 2011
- GO Gages
- NOGO Gages
- Functional Gages
- Calculating to Determine Good Parts Rejected or Bad Parts Accepted
- Steps in the Development of a Dimensional Inspection Plan
23 Tolerance Stack- Up Analysis
- Tolerance Stack- Up Analysis for a Fixed Fastener Assembly
- Rules
- Calculating Gaps; Working the Route
- Calculating Inner and Outer Boundary Means and Their Tolerances
- Plugging the Numbers into the Number Charts
- Calculating Statistical Tolerancing
- Root Sum Squares
- Bender Factor
- Reintegrating the Statistical Tolerancing into the Assembly
- A Simpler Way to Reintegrate the Statistical Tolerance
- More Statistical Formulas and Symbols
- Glossary of Statistical Terms
24 How to be Specific in Calculating and Specifying Statistical
Requirements
for size and Geometric Tolerancing
- Some Useful Definitions When Geometric Tolerances are Used
- Symbology for SPC Formulas
- Arithmetic Mean; Normal Distribution of Tolerance and the Standard
Deviation; Statistical Probability for Tolerance Stack- Up Analysis
for
Positional Geometric Tolerances
- Calculating a Standard Deviation
- Predicting the Amount of Tolerance to be Consumed by Manufacturing
- Charts and Tables
25 Tolerance Stack- Up Analysis in a 5- Part Assembly
- Determining a MIN GAP in a Rotating Assembly
- Factors vs. Non- factors
- Alignment
- Dealing with Threaded Features
- Calculating the Pertinent Numbers
- Simplifying the Assembly Drawing
- Creating a Line Graph with Numbers to Calculate the Minimum
Clearance
- Adding the Negative and Positive Designations
- Wall Thickness Calculations and Choosing the Pertinent Tolerances
- Single Part Analysis
- Using Profile Tol. and Separate Requirements for Accumulated
Error
26 Tolerance Stack- Up Created during Manufacture due to Changing
Set Ups
- Where the Tolerance Accumulation Comes From
- Proportions and Trigonometry
27 GD&T as a Language
- To Properly Read a Drawing
- Reading the Feature Control Frames as Sentences
- Profile
- Tolerance Zones and Pattern Shift Zones
- Reading Two Single Segment Controls
- Using Gages to Visualize a Geometric Tolerance’s Meaning
- Reading a GD&T Sheet
- Optional Tolerancing Approaches for Similar Results
- Gears
- Pattern Shift, Where it Comes From and How it Effects the Workpiece
- Bonus Tolerance, Virtual Condition and Zero Positional Tolerances
- Threads, Gears and Splines
- Sequential Tolerancing Using the Simultaneous Requirement Rule
28 Definitions
|
|
|
|
If you have any questions about GD&T training,
books, workbooks, tests or DVDs,
please reach out to James D. Meadows & Associates, Inc., at (615) 924-3600.
|
© 1997 -
James D. Meadows & Associates, Inc., ALL RIGHTS RESERVED |
Site Design & Maintenance by
VIRTUAL GOLDMINE |
|